U Series Deterministic Polishing Software
U Series Deterministic Polishing Software allows aspheres to be polished to sub-micron specifications faster and easier than ever before. The graphical user interface guides the operator through all aspects of asphere polishing, from initial setup, to characterizing a removal function and performing uniform removal or iterative metrology based figure correction to meet your production requirements.
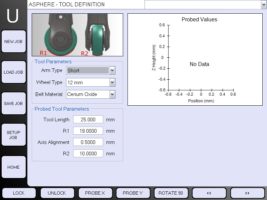
Home Screen
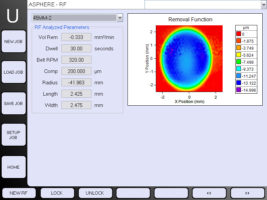
Removal Function Screen
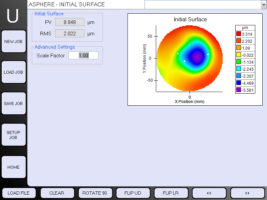
Initial Surface Screen
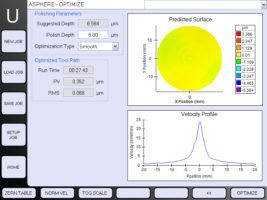
Tool Path Optimization Screen
Features:
Process-Based Job Structure
The layout of U Series allows multiple polishing cycles to exist within the same setup. This allows different polishing cycles to run in succession. For example, a typical job may include two polishing cycles; the first polishing cycle for a bulk material to remove the sub-surface damage left from the grinding operation, and the second performing a figure correction operation that may use a different removal function than the first.
R-Theta Process
The R-Theta process is designed to polish rotationally symmetric spheres and aspheres. During the process, the optic rotates about its optical axis and the UFF polishing tool traverses across its surface from edge to edge. During polishing, the process is capable of removing uniform amounts of material as well as correcting any figure errors to achieve sub-micron accuracies.
Raster Process
The Raster process is designed for polishing flat surfaces with circular or rectangular apertures. During the process, the optic is fixed on the machine (not rotating) and the UFF polishing tool traverses back and forth across the optics surface. The process is capable of removing uniform amounts of material as well as correcting any figure errors on the surface during polishing.
Lens Parameters Screen
The lens parameters screen allows quick and error free entering of the lens prescription. A built-in sag calculator allows an operator to check the surface definition, ensuring accuracy. For advanced users, there are handles to deal with how the optical surface behaves outside of the processing aperture allowing for easier manufacturing of challenging aspheres.
Tool Parameters Screen
The semi-automated tool parameters screen guides the operator through defining the UFF polishing tool. Simple drop down screens and automatic laser probing of the UltraWheel ensure an accurate tool definition.
Removal Function Screen
The removal function screen guides the operator through the entire polishing tool characterization. The steps include setting up and creating the removal function, using on-board metrology to measure the removal function, and then performing any masking and analysis of the measured data.
Initial Surface Screen
The initial surface screen allows an operator to load metrology data for the surface to be polishing if figured correction is desired. U Series supports a variety of both 2D and 3D metrology formats for ease of use. Once uploaded, the operator has the ability to orient the data in relation to how the machine will process it.
Tool Path Optimization Screen
The optimization screen generates the tool path for the optic under polish. The optimization routine relies on the removal function, initial surface quality, as well as information from the user. Upon completion of the calculations, several plots and false color images are displayed, providing the user information on cycle time, predicted surface quality and machine velocity profiles.
The U Series Deterministic Polishing Software is available on the PRO 80 UFF, PRO 160 UFF, UFF 300, and UFF 500 UltraForm® Finishing platforms.